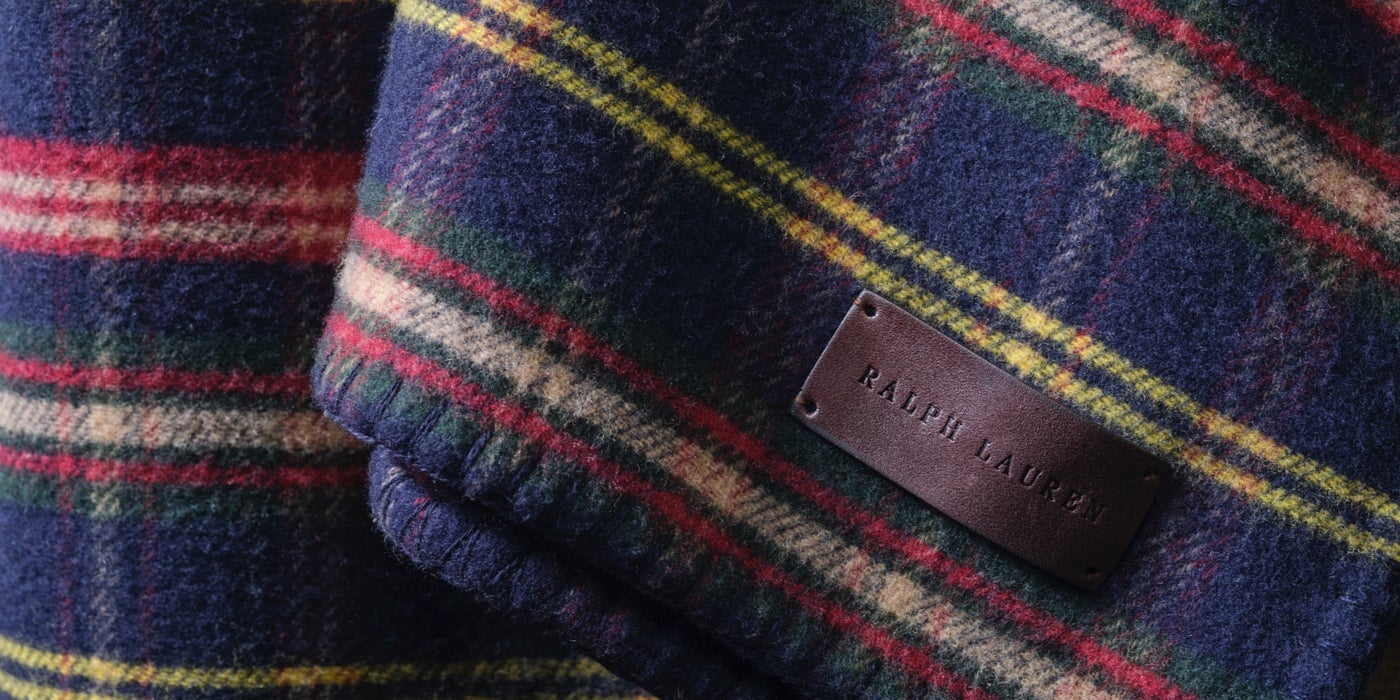
Bringing Home The Heritage
Traditional craftsmanship and a uniquely Ralph Lauren sensibility come together in a capsule collection with famed Scottish mill Johnstons of ElginWhen you hear the phrase “storied Scottish mill,” you probably picture something like this: an idyllic campus on the North Sea coast of Scotland, well-aged chestnut trees and sturdy brick façades, a place where hands young and old are laid on every fiber, every yarn, every fabric. A grassy campus with friendly accents, where the buildings have stood for centuries and a family is still in charge of everything.
And while it might be fun to puncture that cliché, in the case of Johnstons of Elgin, it’s all true.
The story of Johnstons dates back to its founding in 1797 in the seaside town of Elgin, and you can still visit the original mill building if you’re fortunate enough to travel there in person. Despite the years, much remains the same, with relationships whose longevity can be counted in centuries. For example, Johnstons has supplied Estate Tweed and Tartan to Gordon Castle since the 1800s. (It’s an inspiring arrangement—in exchange, Gordon provides gin to the mill.)
This intimacy, and emphasis on old-world ways of doing business, somehow feels very right in 2021. By sourcing its materials locally rather than globally, for instance, Johnstons reduces its impact on the planet—an effort recognized by the royal family, which bequeathed The Queen’s Award for Enterprise: Sustainable Development to the brand earlier this year, a prestigious prize honoring Johnstons’ environmental stewardship.
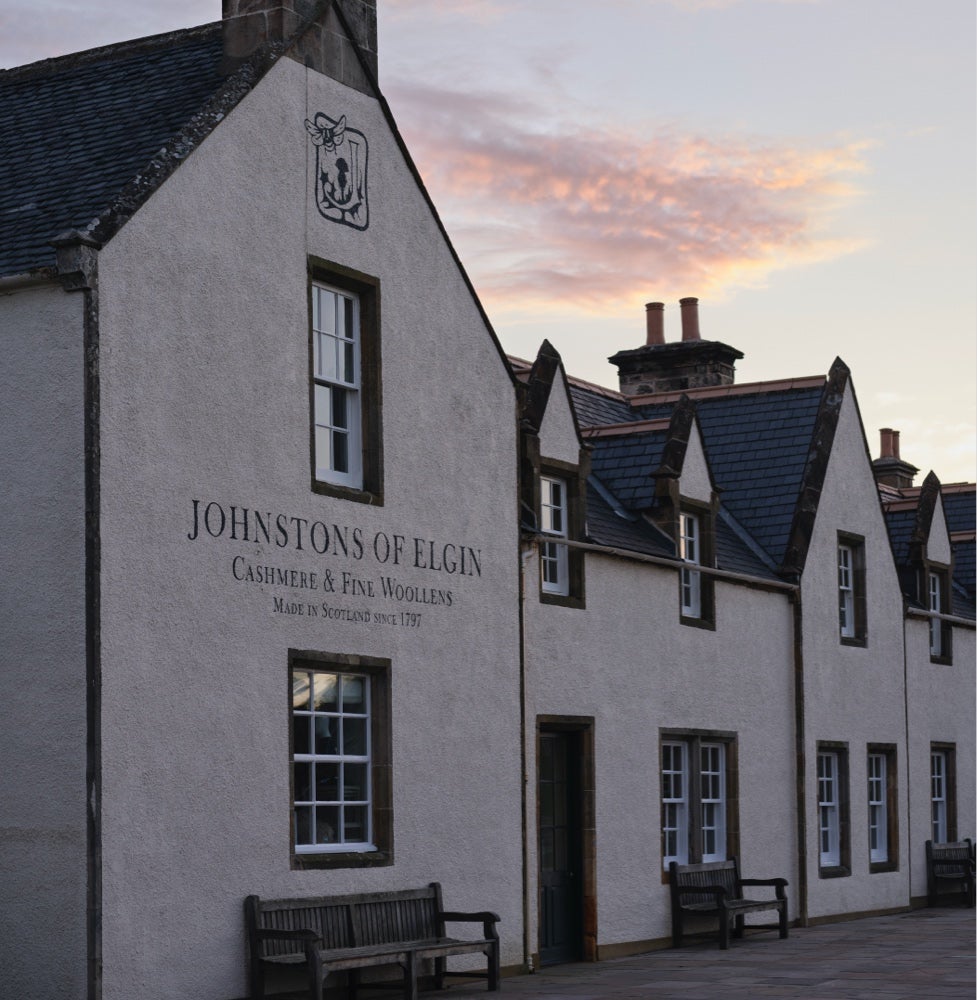
Today, it’s the last fully vertical mill in Scotland, meaning it’s the only place where woolen fabrics are created entirely in-house, all on that picturesque campus near the sea. And while much of the work is still done the old-fashioned way—some of the dyes used date back to 1856—Johnstons has also embraced what technology has to offer. For example, jacquards that once were designed through a painstaking hand-painting process, taking months to develop, can now be done by computer, while still producing the same breathtaking results.
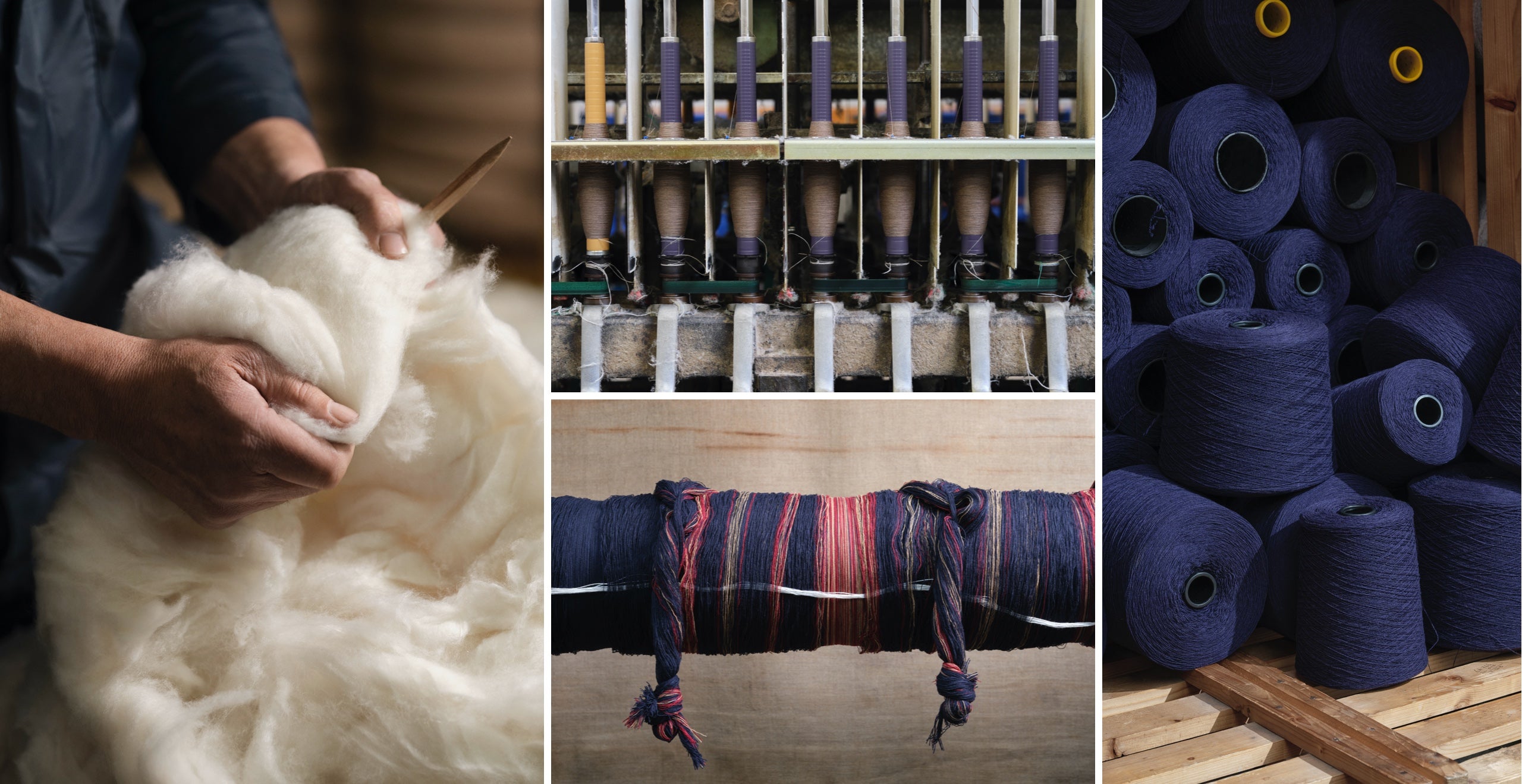
Suffice it to say, this history and heritage made Johnstons a natural fit for Ralph Lauren, and why this season Ralph Lauren Home partnered with Johnstons on a new collection of four throw pillows and four throw blankets. Each is crafted entirely in the storied mill using traditional processes, with patterns that allude to traditional Scottish tartans, and features a unique double-facing fabric, ensuring the inside of a pillowcase is as beautiful as the outside.
“With Ralph, the main thing between our two companies is the authenticity of what we do,” says Louise Sullivan, design manager at Johnstons of Elgin. Similarly, the companies share a philosophy of respecting traditions while embracing innovation. “We innovate but at the same time remain true to the crafts—we can’t actually make our product without those crafts or craftspeople,” she adds.
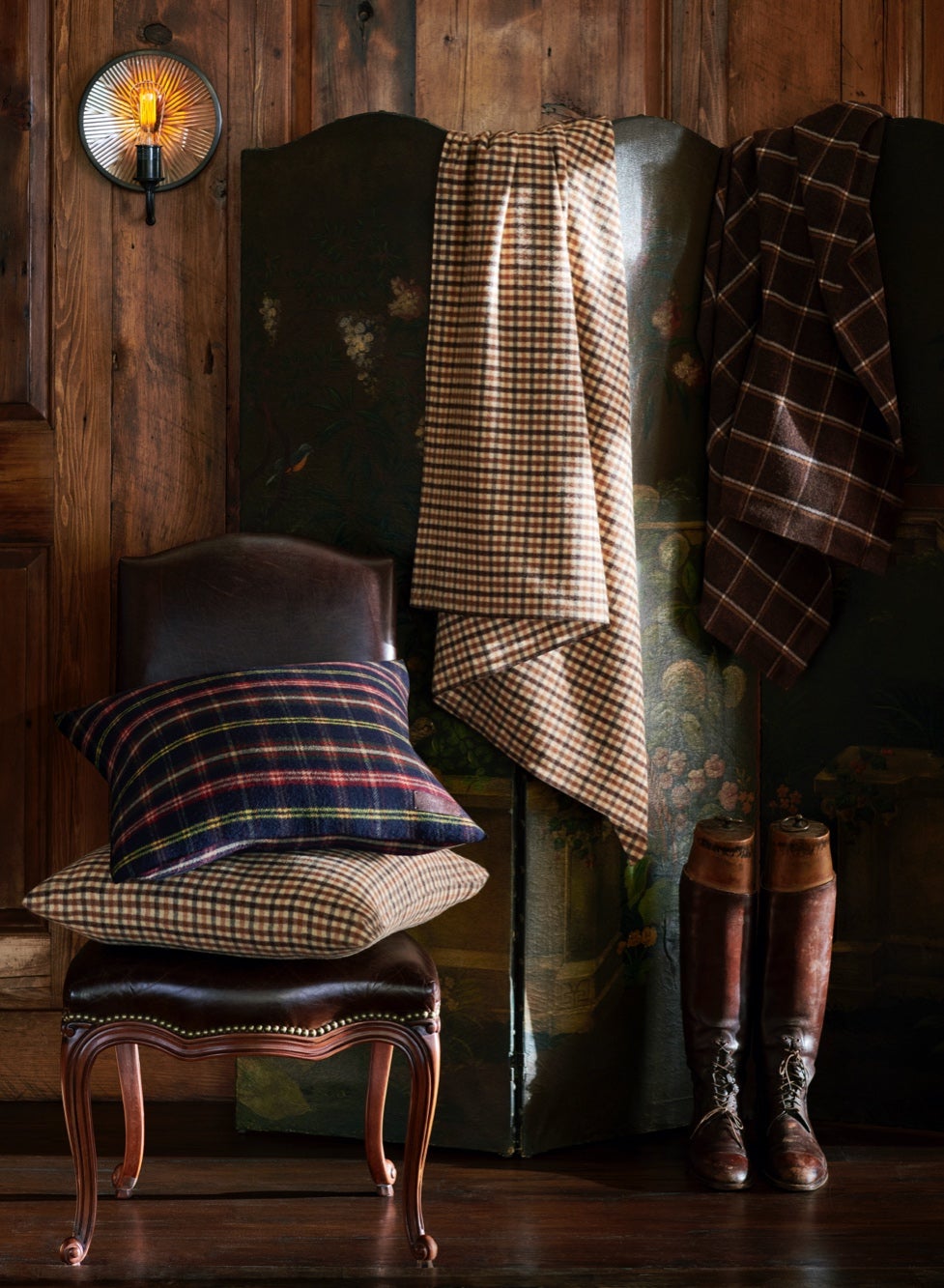
Once completed, each pillowcase and blanket is the product of 30 “processes,” or individual steps within a broader overall process of turning raw fiber into a final product. It all begins with dyeing those fibers, and Johnstons has created roughly 7,500 shades over its lifetime. The next step is called blending and carding, in which fibers are mixed together—sometimes to blend colors, other times to blend, say, merino wool and cashmere—before being loaded by hand into a carding machine, which combs the fabric to straighten the fabrics. (One such carding machine served Johnstons from 1868 through 1993.) Next comes spinning, in which the fibers are twisted together to strengthen them—another process that is carefully supervised by hand. This is followed by weaving, in which a weft yarn—the one that runs perpendicular to vertical threads in the spun cloth—is woven using a loom, a process that creates custom plaids like the ones found exclusively in this Ralph Lauren Home collection. Next comes knitting, in which fabrics are sewn together to create a piece (like a throw blanket) after being washed and milled using local water. Each fabric is then finished, which includes being “scoured” (cleaned) with soft Scottish water, which helps return it to its soft, natural state, and then dried by being rolled by a Tentering machine. (Think of it as a huge, industrial-sized dryer.)
After all that, there are still some additional finishing touches, like sewing on the leather “Ralph Lauren” patch. Taken together, you have the kind of unique, inviting decorative accessories that truly makes a house a home—all in a custom plaid that invokes Scottish history while feeling quintessentially Ralph Lauren.
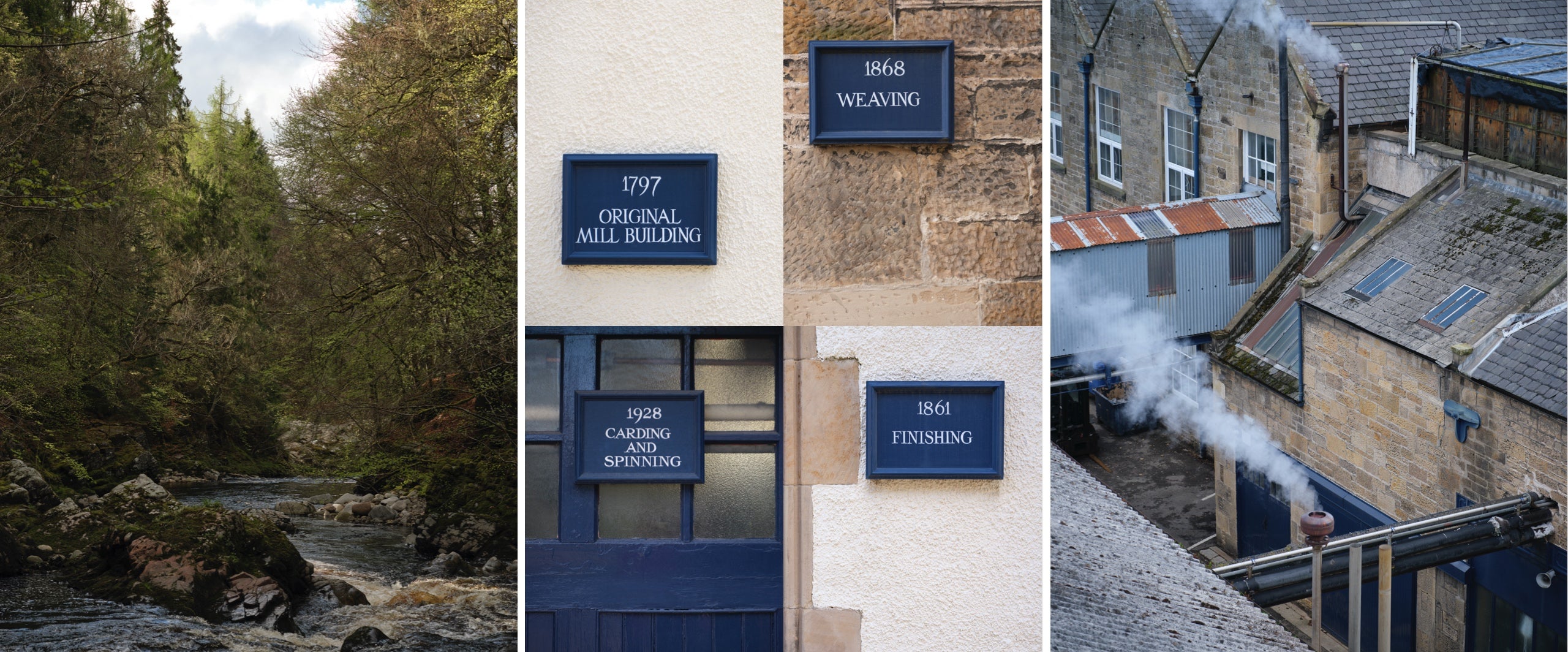
- © Ralph Lauren Corporation
- Photographs courtesy of Tom Bunning