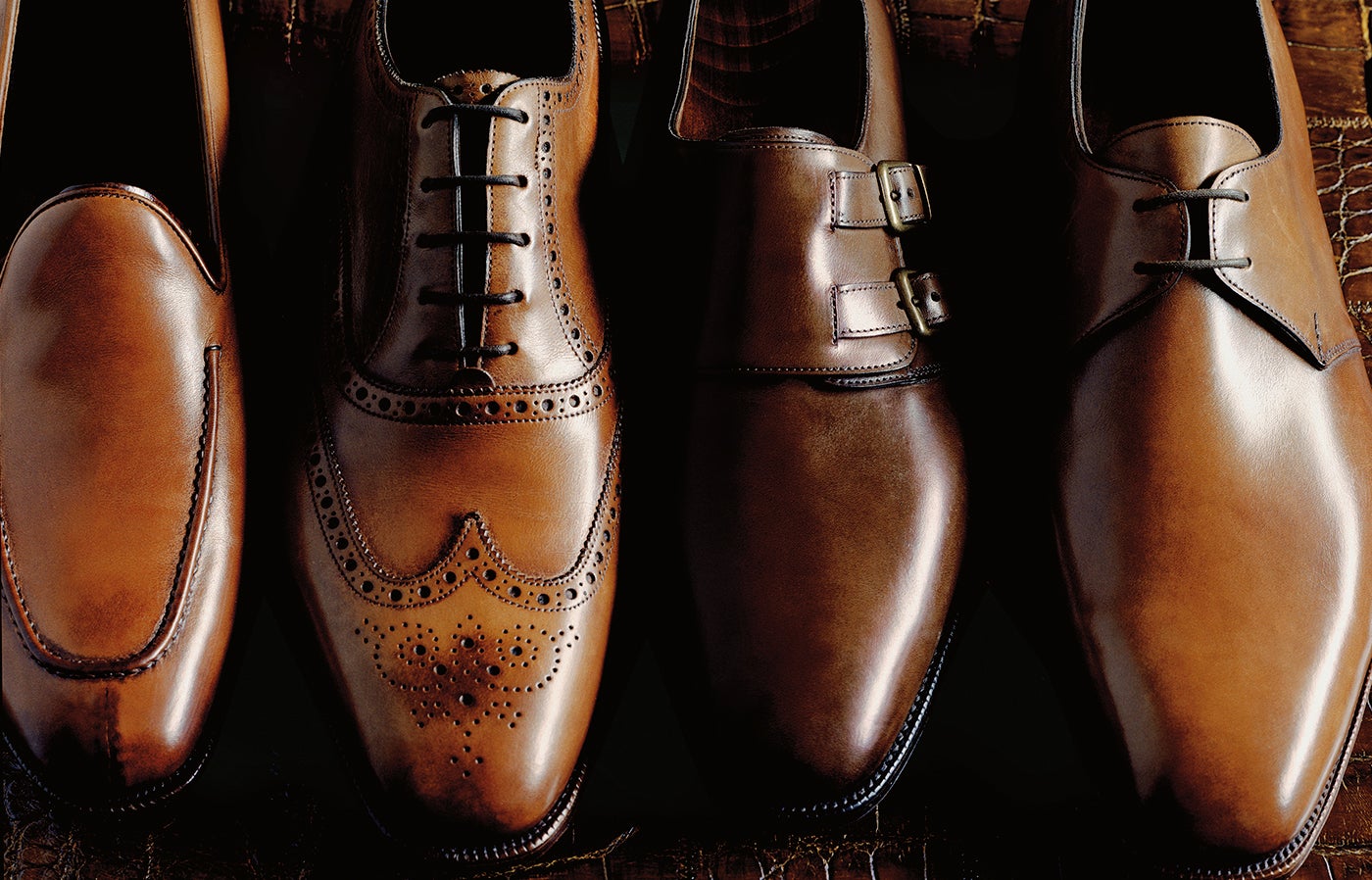
About 65 miles northwest of London lies the town of Northampton, widely known as the shoemaking capital of England, and possibly the world. It’s there that Ralph Lauren’s finest footwear—that bearing the legendary Purple Label stamp—is made by hand, by master craftsmen in an area so esteemed that at least one of London’s finest hotels has sent its butlers there to learn the proper method of polishing a shoe.
Purple Label footwear from Northampton is benchmade, which means that it’s crafted by hand, over a period of up to three weeks, resulting in some of the most elegant and longest-lasting shoes money can buy.
The whole process begins with a sketch, used to illustrate exactly how Mr. Lauren envisions the finished shoe, from the shape of the toe and heel to the final burnishing and decoration. To bring that sketch to life, the finest leathers are chosen, then carefully examined for any imperfections.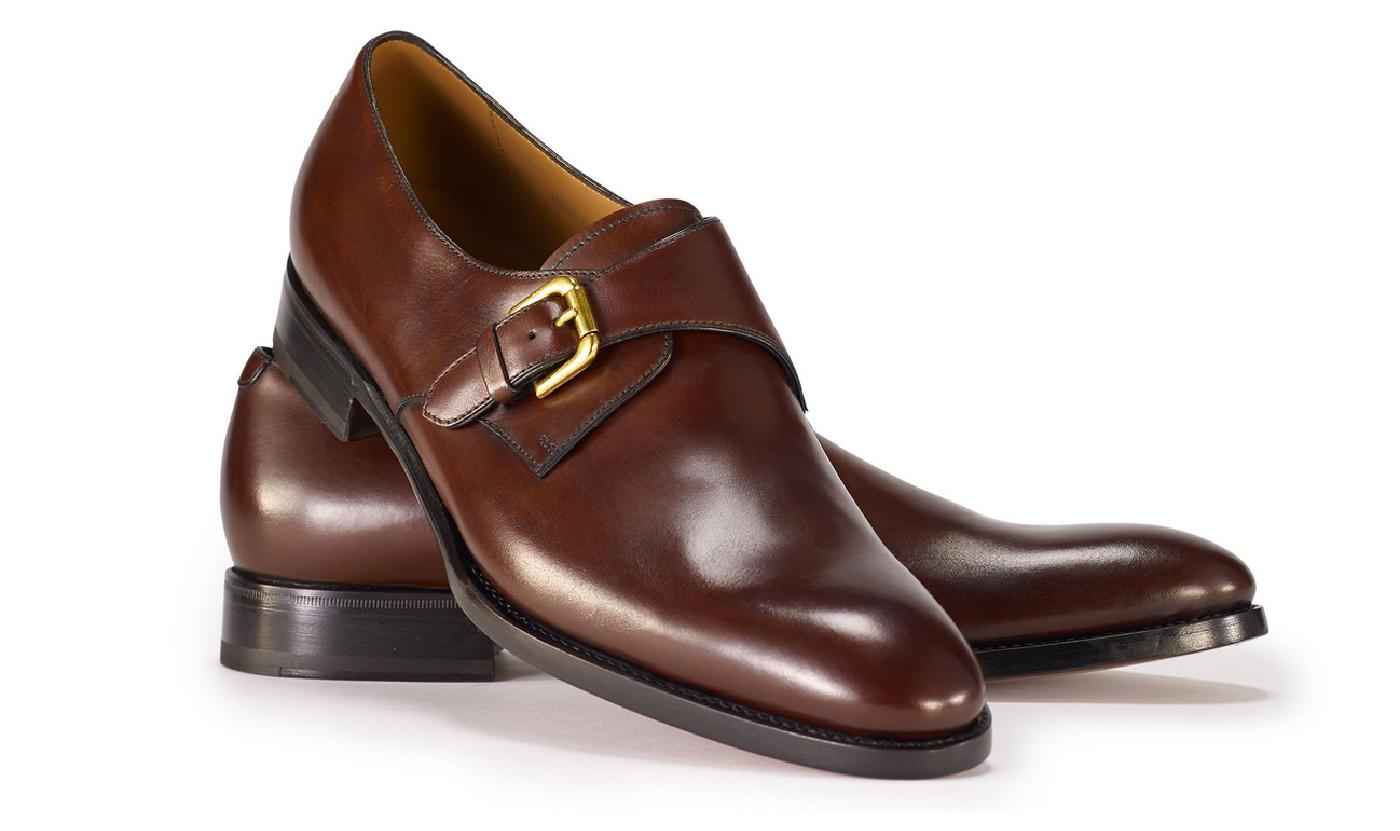
The material is then trimmed and sewn together by hand to form each shoe. Our craftsmen use a waxed cotton thread, often attached to a boar’s bristle. This allows for a smaller, more uniform hole and more precise construction. We also use Goodyear welting—a 19th-century technique for attaching the sole of a shoe to the upper. The upper is stitched to the welt (the piece of leather that runs along the outsole), which is then stitched to the sole, all using what is called a Goodyear welting machine. (A layer of ground cork is added to the sole, and the leather is skived right before this happens, to ensure greater comfort and a more refined presentation.) This means your shoes can be resoled endlessly—it’s not uncommon for a pair of benchmade, Goodyear-welted dress shoes to last for decades.
Finally, each pair is stained, burnished and polished by hand, before having an exclusive pattern heat-stamped onto the sole.
For a step-by-step look at the process, click through the slideshow below.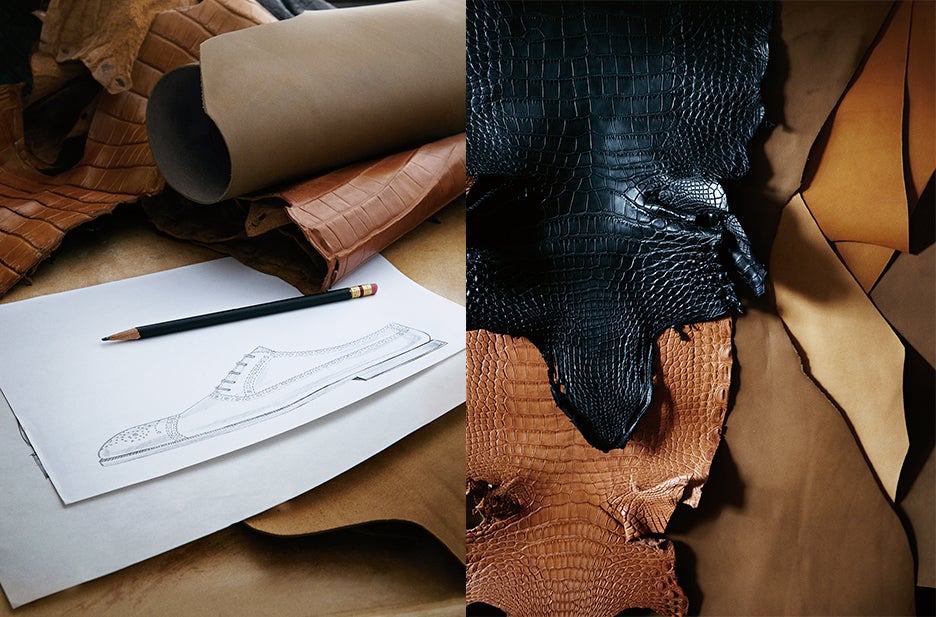
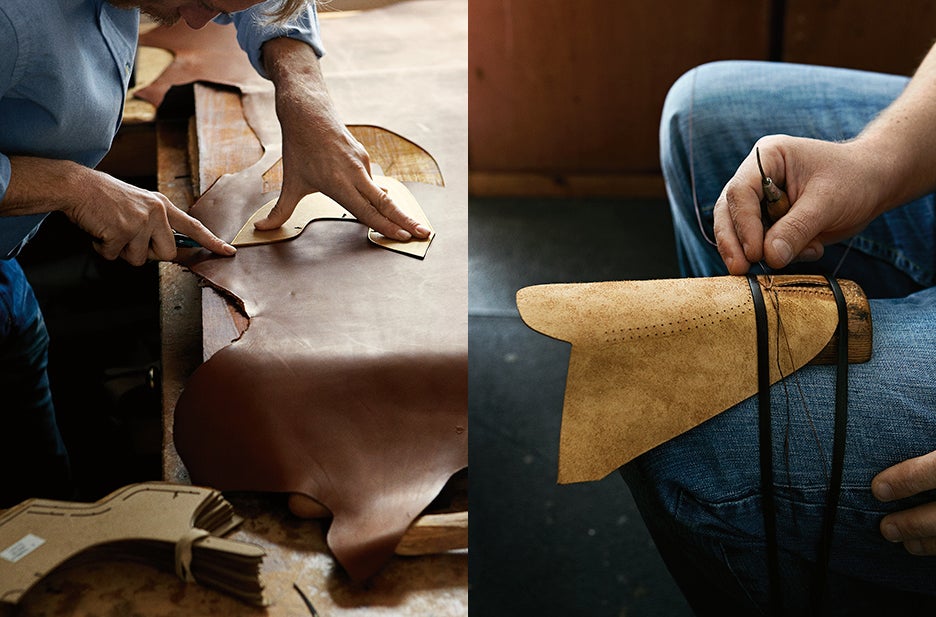
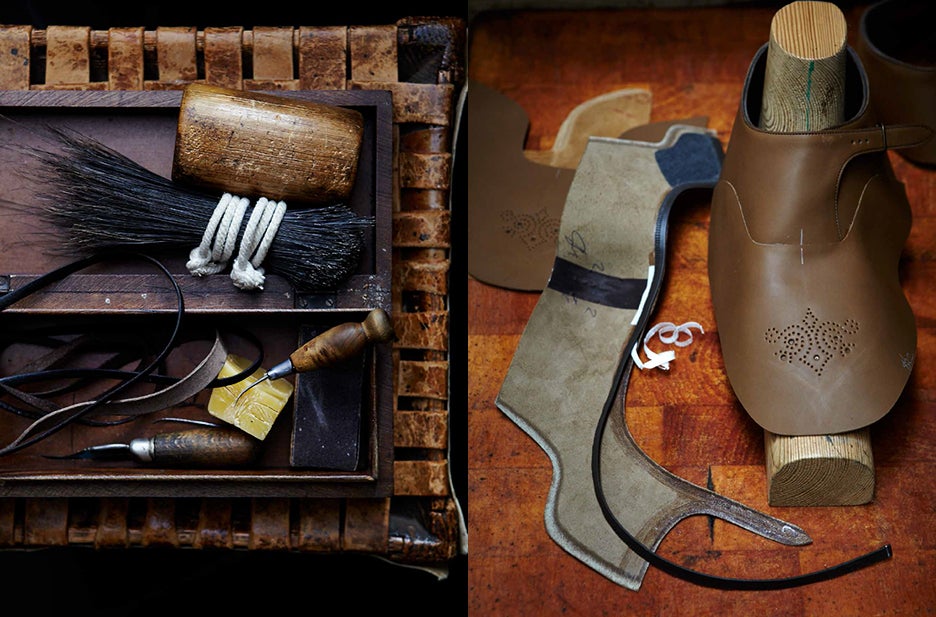
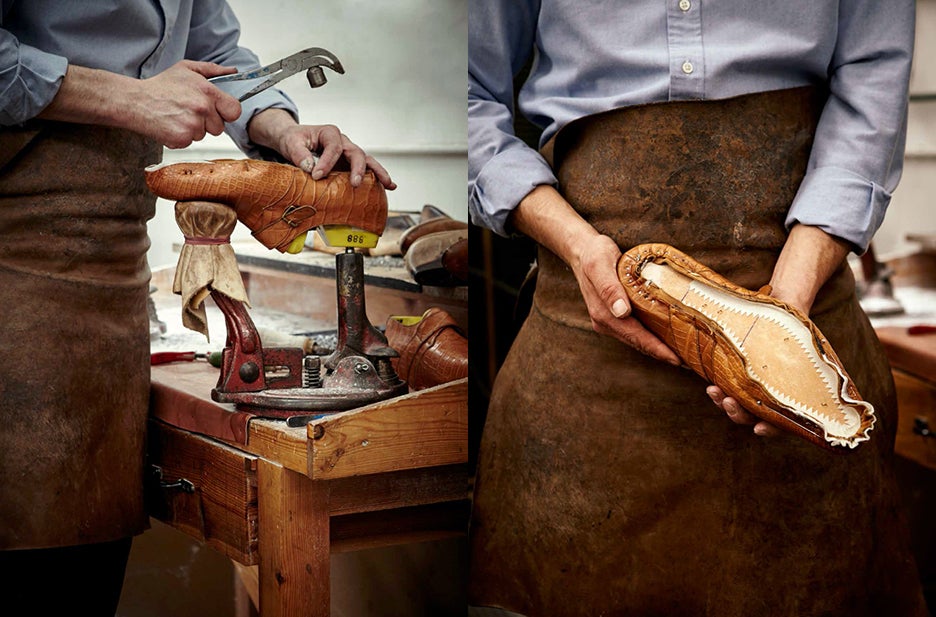
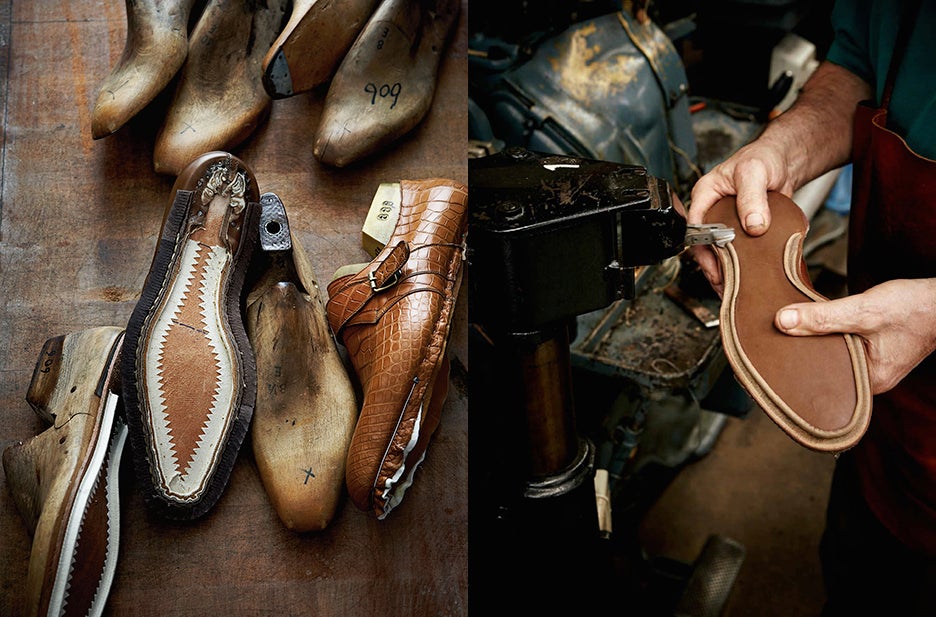
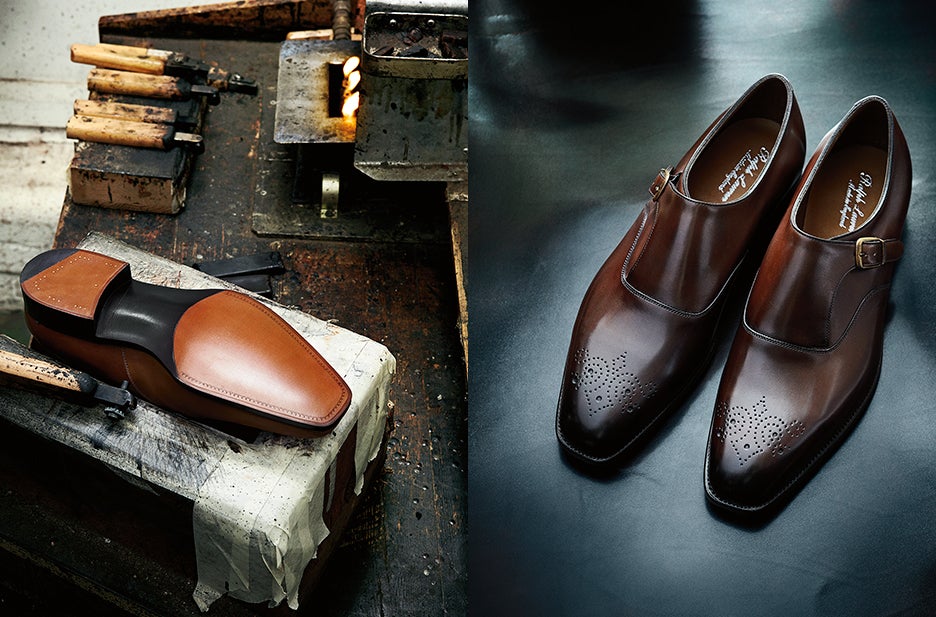
- ALL PHOTOGRAPHS COURTESY OF RALPH LAUREN CORPORATION